Kaizen Training & Certification (Live Online)
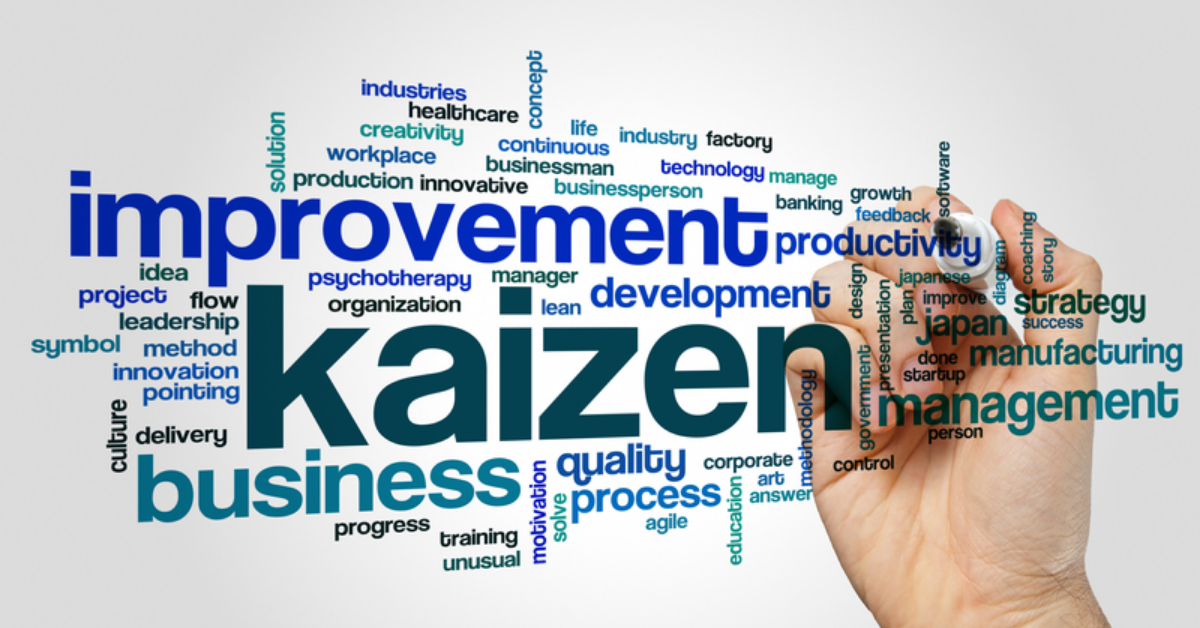
About Course
Elevate Your Career with KAE Education’s Kaizen Training & Certification Course
The Kaizen Training & Certification Course offered by KAE Education is a dynamic program designed to provide participants with the skills and knowledge needed to drive continuous improvement using proven Kaizen methodologies. This 8-hour training is a perfect blend of theory and hands-on learning that enables professionals to enhance process efficiency, reduce waste, and boost customer satisfaction.
Course Overview
KAE Education’s Kaizen Training covers essential aspects of the Kaizen philosophy and its real-world applications. The curriculum is carefully structured to give participants a well-rounded understanding:
(i) Introduction to Kaizen:-
Learn the history, principles, and global impact of Kaizen, focusing on its role in continuous improvement.
(ii) Kaizen Tools & Techniques:-
Master tools such as 5S, Value Stream Mapping, and Root Cause Analysis to identify and eliminate waste.
(iii) Continuous Improvement Processes:-
Develop strategies to implement long-term improvement processes within an organization.
(iv) Change Management:-
Explore how to manage organizational change effectively, ensuring minimal resistance and smooth transitions.
(v) Team Collaboration:-
Foster a work environment where all team members actively contribute to improvement initiatives.
(vi) Problem-Solving Skills:-
Sharpen your ability to identify problems, analyze root causes, and develop effective solutions.
(vii) Performance Metrics:-
Understand how to measure success using Key Performance Indicators (KPIs) and track progress over time.
(viii) Real-World Applications:-
Case studies and a practical capstone project allow participants to apply Kaizen principles in realistic Business scenarios.
Benefits of Enrolling in Kaizen Training
(i) Expert Instruction:-
Learn from seasoned professionals with extensive experience in Kaizen and process improvement.
(ii) Hands-on Learning:-
Engage in interactive exercises and simulations, including a capstone project to implement Kaizen principles.
(iii) Comprehensive Curriculum:-
Gain a well-rounded understanding of the tools, techniques, and principles needed for continuous improvement.
(iv) Career Support:- Receive guidance on leveraging your new skills in the Job market with Resume and Interview assistance.
Future Career Prospects
Completing the Kaizen Training & Certification Course opens doors to various career paths. Here are a few roles participants can pursue:
(1) Continuous Improvement Manager
(2) Lean Manufacturing Specialist
(3) Quality Assurance Manager
(4) Operations Manager
(5) Process Improvement Consultant
(6) Project Manager
(7) Business Analyst
(8) Supply Chain Manager
Industry Applications
Kaizen principles can be applied across Industries such as:
(i) Manufacturing:-
Improve production processes, reduce waste, and boost product quality.
(ii) Healthcare:-
Streamline operations and enhance patient care while reducing costs.
(iii) Retail:-
Optimize inventory management and improve customer service.
(iv) Finance:-
Enhance financial processes to reduce errors and increase service efficiency.
(v) Technology:-
Apply continuous improvement strategies to enhance software development and IT operations.
FAQs:
Q. What is Kaizen Training?
Ans. Kaizen training focuses on continuous improvement and process optimization to reduce waste and boost efficiency.
Q. How long is the Kaizen course?
Ans. The course lasts 8 hours, packed with valuable content and hands-on learning.
Q. Do I receive certification upon completion?
Ans. Yes, you’ll receive a Kaizen Certification from KAE Education after successfully completing the course.
Q. Is this course suitable for all Industries?
Ans. Yes, Kaizen principles are applicable across various Industries, including Manufacturing, Healthcare, Retail, Finance, and Technology.
Q. What roles can I pursue after this course?
Ans. You can pursue roles like Continuous Improvement Manager, Lean Manufacturing Specialist, and Quality Assurance Manager.
Q. Are there hands-on projects?
Ans. Yes, the course includes practical exercises and a capstone project to apply Kaizen principles in real-world scenarios.
Q. What tools will I learn in the course?
Ans. You will learn key Kaizen tools such as 5S, Value Stream Mapping, and Root Cause Analysis to drive continuous improvement.
Conclusion
KAE Education’s Kaizen Training & Certification Course is an invaluable resource for professionals aiming to lead continuous improvement within their organizations. With its comprehensive curriculum and real-world applications, participants will be well-prepared to implement Kaizen methodologies and drive operational excellence. This course is a strategic investment in your career, equipping you to lead change, enhance efficiency, and ensure long-term success in any Industry.
To enroll in Kaizen Training: Click here
To know more about Kaizen Technique: Click here
Course Content
Module 1: Introduction to Kaizen
-
Overview of Kaizen
-
Importance of process improvement
-
Setting process improvement objectives